By consolidating the EV drivetrain, Donut Lab believes the industry can unlock next-gen performance and significant cost savings. By Will Girling
Since the electric vehicle (EV) powertrain and drivetrain have significantly fewer moving parts relative to internal combustion engine models, it is simpler and more cost effective to manufacture and maintain. Nonetheless, some players believe it is still far from optimal. “Everyone in the industry hates the drivetrain and power transmission,” states Marko Lehtimäki, Chief Executive and Co-Founder of Donut Lab. “From motor to wheels, there’s up to 200 parts taking up a lot of space and adding cost, weight, and complexity.”
His company originated with the goal of developing a modular platform that could fundamentally change how EVs are built. Around 2019, Lehtimäki determined that an electric two-wheeler presented the ideal starting point: a challenging form factor that requires squeezing a lot of power, torque, and range into a small package. This led to the formation of Verge Motorcycles, which developed a streamlined and powerful in-wheel motor to eliminate the complexities of modern powertrains.
By November 2024, following discussions with “leading OEMs”, Lehtimäki recognised the opportunity of broadening this motor’s applicability across the automotive industry. Donut Lab was subsequently spun off to accelerate and advance a range of next-gen powertrain technologies, including hardware and software.
Changing vehicle dynamics
Until recently, the EV segment had avoided incorporating in-wheel motors due to their unfavourable power-to-weight ratio, which increased unsprung mass and negatively impacted handling and performance. “Our thinking was that if this could be solved, then we could change the whole concept of motor-to-wheel power transmission,” explains Lehtimäki. This led directly to the creation of the Donut Motor.
Comparing the iterative process to semiconductor optimisation in digital systems, he states that Donut Lab has been able to increase the Donut Motor’s performance while making the unit progressively smaller. “We’ve boosted efficiency relative to weight and done so with a smaller bill of active materials—the ones that create all the cost.” The 21-inch ‘Automotive spec’ in-wheel motor outputs 630kW of power and 4,300Nm of torque from a 40kg unit. In an industry where competitors generally prioritise either power or torque density, the company claims its solution excels in both, making it one of the most powerful e-motors in the world.
It didn’t take long to establish the real-world potential for passenger cars. During a hyper car project with an unspecified automaker, the Donut Motor shaved 108kg from the vehicle’s original weight (1,450kg), reduced powertrain expenditure by 55%, and unlocked 200 litres of extra space. “Hyper car manufacturers pay a lot of money to save 100g, let alone 100kg,” Lehtimäki emphasises. Similar results were also achieved in a compact SUV project.
The design, he adds, is fully patented and wholly unique in its capabilities. “We’re able to achieve highly advanced motor control—more than 100 times per second, or up to ten times faster than ABS in either accelerating or braking.” Lehtimäki proposes that this level of performance could fundamentally alter how engineers consider driving dynamics: “In the future, we could see fully digital, software-defined dynamics that could make an SUV handle like a sports car.”
Out of the box functionality
In addition to cars, the Donut Motor’s symmetrical design means it can be scaled up and down linearly for a variety of EV specs: drones, scooters, motorcycles, and semi-trucks. Regarding the latter, a case study found that using six 21-inch in-wheel motors with 200kW of power and 3,000Nm of torque each could significantly impact the operational value of e-trucks. Donut Lab managed to reduce the vehicle’s bill of materials by €15,000 (US$15,525) and remove around 1,100kg of weight from the drivetrain, motors, inverters, and battery.
The ability to carry more cargo and improve margins could prove vital for the transport segment as it electrifies—the electric powertrain’s added weight compared to diesel currently makes it less attractive for certain use cases. Furthermore, Lehtimäki believes all segments could benefit from the “design freedom” that Donut Motor affords. “EV platforms can have a highly desirable flatbed design. Automakers place the battery modules where they want and motors in the wheels—all that’s left is wiring, and the core vehicle is ready.”
He reports that industry interest has been strong so far, and production on the ‘family’ of in-wheel motors is already underway. However, Donut Lab also strives to provide a complete EV technology ecosystem for automakers that might require a more holistic solution. This product stack will include a high-efficiency, modular architecture battery; a “next-gen, high-performance” compute unit ready for artificial intelligence, advanced connectivity, and sensor tech; and smart software to facilitate over-the-air updates and cloud-based telematics. The idea, according to Lehtimäki, is to provide “out of the box” functionality that boosts automakers’ go-to-market strategies by saving time and money on R&D.
Building better EVs
While Donut Lab holds an ambitious vision for the future of e-mobility, Lehtimäki concedes that there will likely be obstacles. The global electric powertrain market is forecast to grow from US$97bn in 2023 to US$230.5bn by 2030, according to MarketsandMarkets. A large and growing sector may not react well to the prospect of component consolidation, and suppliers may lean on their relationships with OEMs to oppose the technology. He also believes some companies might initially reject in-wheel motors that were not developed in-house. “But that’s a general industry attitude unrelated to our specific products.”
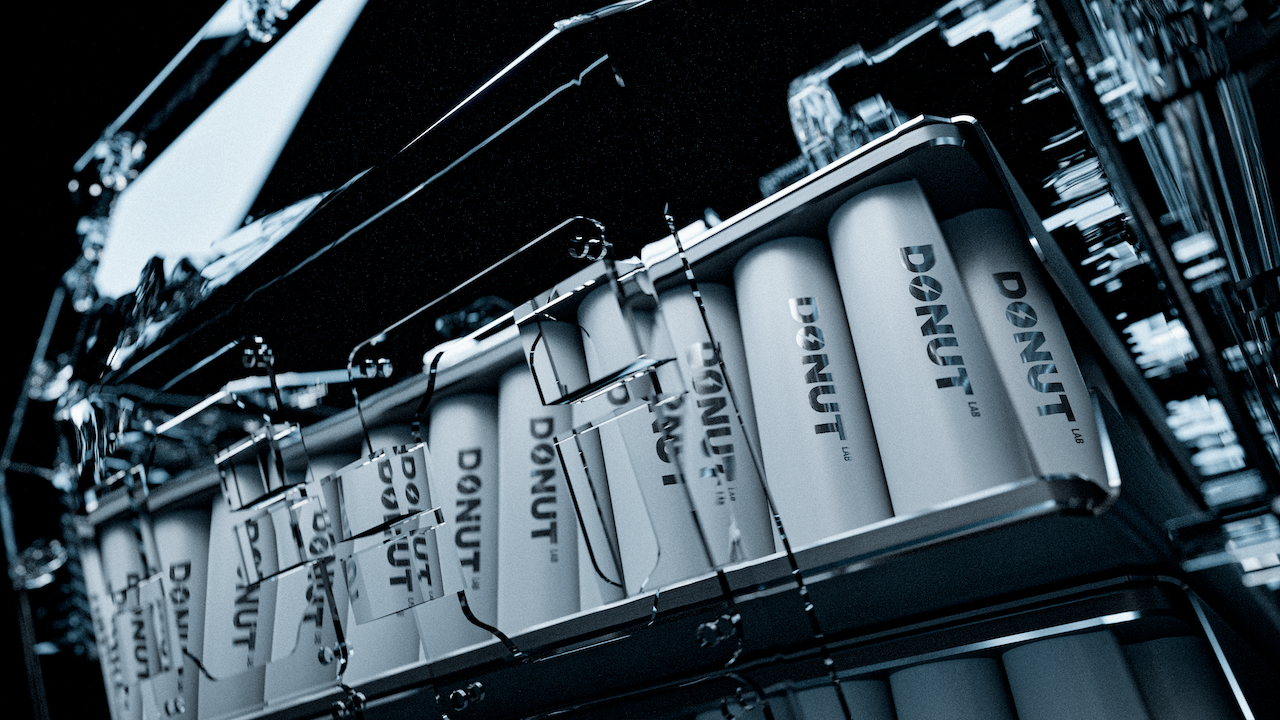
Nonetheless, enthusiasm for the Donut Motor continues to grow, with many media outlets highlighting its appearance at CES 2025 in January. “I’m predicting a snowball effect: in 18 months, when some smaller volume OEMs have integrated our technology, I think bigger players will take more notice,” says Lehtimäki. As US and European automakers search for opportunities to equal and surpass China’s achievements in EV manufacturing, they may find the value proposition of in-wheel motors highly compelling.
Indeed, aside from Tesla, few Western brands can produce EVs profitably, with e-mobility business arms sometimes haemorrhaging billions of dollars per year. This is primarily because EVs remain too expensive to generate the sales volumes necessary to capitalise on high margins, causing some to initiate strategic reversals in 2024. “This is a challenge that nearly all manufacturers are facing, and saving 20% on the bill of materials for the powertrain could be enough to determine whether an EV is profitable or not,” concludes Lehtimäki. “Going after higher efficiency is ultimately how the industry will build better EVs.”